Title: Understanding the CNC Programming Process
In modern manufacturing, Computer Numerical Control (CNC) has revolutionized the way various parts and components are produced with high precision and efficiency. CNC programming lies at the heart of this process, where instructions are coded to dictate the movements of machines. Let's delve into the comprehensive process of CNC programming:
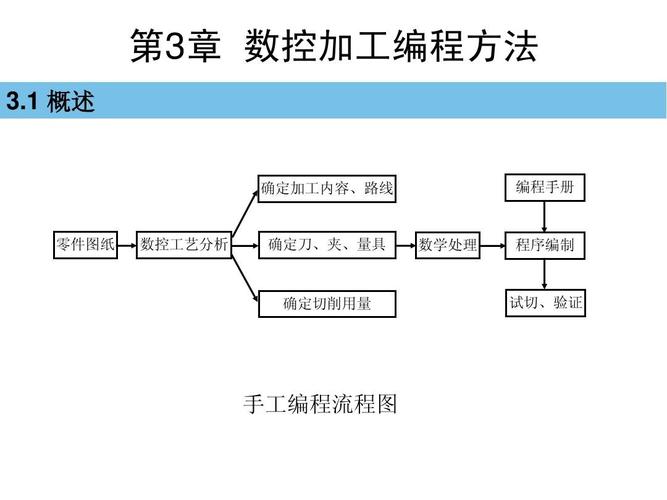
1. Design Phase:
CAD (ComputerAided Design):
The process typically starts with creating a 2D or 3D model of the part to be manufactured using CAD software. This digital design serves as the blueprint for the CNC program.
CAM (ComputerAided Manufacturing):
Once the design is finalized, CAM software is employed to generate the toolpaths necessary for machining operations. CAM software considers factors like tool selection, cutting speeds, and feeds to optimize the manufacturing process.2. Programming Phase:
Selecting the Programming Language:
CNC machines use different programming languages, such as Gcode and Mcode, to communicate instructions. Gcode, the most common language, controls the movement and speed of the machine, while Mcode directs auxiliary functions like tool changes or coolant activation.
Writing the Program:
The CNC programmer translates the design and manufacturing requirements into a series of commands understandable by the CNC machine. This involves specifying toolpaths, cutting parameters, tool changes, and any necessary auxiliary functions.
Simulation:
Before running the program on the actual machine, it's crucial to simulate the toolpath using specialized software. This helps identify any potential errors or collisions that could occur during machining.3. Machine Setup:
Material and Tool Preparation:
The appropriate raw material is loaded onto the CNC machine, along with the required cutting tools. Tools must be correctly installed and calibrated to ensure precision during machining.
Workpiece Fixturing:
The workpiece is securely clamped or fixtured onto the machine bed to prevent movement during machining. Proper fixturing is essential for maintaining accuracy and repeatability.4. Program Transfer:
Loading the Program:
The CNC program, typically stored on a USB drive or transferred electronically, is loaded into the CNC machine's control unit.
Program Verification:
Before running the program, operators may perform a final verification to ensure that the correct program has been loaded and that all parameters are set correctly.5. Machining Operations:
Execution:
Once everything is set up and verified, the CNC machine begins executing the programmed instructions. This involves precisely controlling the movement of the cutting tool along the designated toolpaths to shape the workpiece according to the design.
Monitoring:
Operators closely monitor the machining process, checking for any anomalies, tool wear, or deviations from the expected results.6. PostProcessing:
Quality Inspection:
After machining is complete, the finished parts undergo inspection to verify dimensional accuracy and surface finish. This may involve using measurement tools such as calipers, micrometers, or coordinate measuring machines (CMMs).
Documentation:
Documentation of the machining process, including tooling used, cutting parameters, and any deviations encountered, is essential for quality control and future reference.7. Optimization and Iteration:
Process Improvement:
Based on the results of the machining process and feedback from quality inspection, adjustments may be made to the CNC program or machining parameters to optimize efficiency and quality.
Iterative Refinement:
Continuous improvement is key in CNC programming, with programmers and operators refining processes over time to achieve better results and productivity.In conclusion, CNC programming is a systematic process that involves translating design specifications into machinereadable instructions, setting up the CNC machine, executing the machining operations, and verifying the quality of the finished parts. By following best practices and continuously refining processes, manufacturers can harness the full potential of CNC technology to produce highquality components efficiently and costeffectively.
Feel free to reach out if you have further questions or need clarification on any aspect of CNC programming!
版权声明
本文仅代表作者观点,不代表百度立场。
本文系作者授权百度百家发表,未经许可,不得转载。