Title: Understanding the CNC Programming Process
Creating CNC (Computer Numerical Control) programs involves a series of steps that ensure precision, efficiency, and safety in machining operations. Let's delve into the detailed process of CNC programming:
1. Design and CAD Modeling:
Begin with a clear understanding of the part to be machined.
Utilize ComputerAided Design (CAD) software to create a detailed 3D model of the part.
Ensure the model accurately represents the final product, including dimensions, tolerances, and surface finishes.
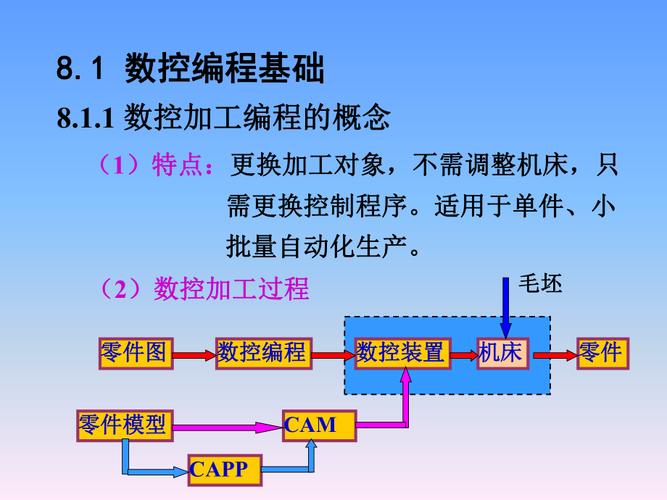
2. CAM Programming:
Convert the CAD model into machinereadable instructions using ComputerAided Manufacturing (CAM) software.
CAM software generates toolpaths based on factors such as tool geometry, material properties, and machining strategy.
Select appropriate cutting tools and machining parameters for each operation.
3. Toolpath Generation:
CAM software calculates the toolpath, specifying the exact movements of the cutting tool.
Consider factors like tool clearance, avoiding collisions, and minimizing machining time.
Optimize toolpaths to achieve the desired surface finish and dimensional accuracy.
4. PostProcessing:
Translate the toolpath data into a format compatible with the specific CNC machine.
This involves converting CAM output (Gcode) into machinespecific language (Mcodes and Gcodes) using a postprocessor.
Ensure compatibility with the machine's controller and capabilities.
5. Simulation and Verification:
Use simulation software to visualize the machining process and detect any errors or collisions.
Verify toolpaths, clearances, and machining sequences to prevent costly mistakes.
Confirm that the program matches the intended design and machining requirements.
6. Program Transfer:
Transfer the validated CNC program to the machine's control unit.
Options for transfer include direct connection, USB drive, or network transfer.
Ensure the program is stored securely and labeled accurately for future reference.
7. Machine Setup:
Prepare the CNC machine for machining operations.
Install the appropriate cutting tools, workholding fixtures, and tool offsets as specified in the program.
Verify machine alignment, tool lengths, and part zero positions.
8. Machining Operations:
Execute the CNC program to machine the part.
Monitor the process for any anomalies, adjusting feeds and speeds as necessary.
Conduct periodic inspections to ensure quality and accuracy throughout the machining process.
9. PostMachining Tasks:
Perform postmachining tasks such as deburring, cleaning, and inspection.
Measure machined parts using precision instruments to verify dimensional accuracy.
Document any deviations from the intended specifications for future reference.
10. Program Optimization and Iteration:
Analyze machining performance and identify opportunities for optimization.
Adjust cutting parameters, tool selection, or machining strategies to improve efficiency and quality.
Iterate on the CNC program based on feedback and lessons learned from previous machining cycles.
Conclusion:
CNC programming is a systematic process that involves design, programming, simulation, and machining.
By following best practices and utilizing advanced CAM technologies, manufacturers can achieve high precision, efficiency, and repeatability in their machining operations.
Continuous improvement and adaptation are essential for optimizing CNC programs and staying competitive in today's manufacturing landscape.
This comprehensive approach to CNC programming ensures that machined parts meet design specifications while maximizing efficiency and minimizing errors. Embracing the latest advancements in CAD/CAM software and machining technology empowers manufacturers to deliver highquality components with speed and accuracy.
版权声明
本文仅代表作者观点,不代表百度立场。
本文系作者授权百度百家发表,未经许可,不得转载。