机床编程原点
优化机床编程顺序的指导建议
在机床编程中,优化编程顺序是确保生产效率和产品质量的关键。合理的编程顺序可以最大限度地减少加工时间、减少切削力和工具磨损,并最大程度地提高生产效率。以下是一些建议,帮助您优化机床编程顺序:
1. 工序分析和优化
在开始编程之前,进行工序分析是至关重要的。这包括:
确定加工的具体工艺和步骤。
评估每个工序的加工难度和时间。
确定可能的瓶颈和优化机会。
2. 合理的刀具选择
选择合适的刀具对于优化编程顺序至关重要。考虑以下因素:
材料的类型和硬度。
切削条件(如切削速度、进给率等)。
加工表面的精度和表面质量要求。
3. 分层加工策略
采用分层加工策略可以减少加工过程中的切削力和工具磨损,提高加工效率。这包括:
粗加工:使用粗加工刀具快速去除大量材料。
半精加工:采用适当的刀具和参数进行中等量的材料去除。
精加工:使用细加工刀具进行精细加工,提高表面质量和尺寸精度。
4. 先粗后精的原则
遵循先粗后精的原则有助于减少加工时间和工具磨损。在粗加工阶段,可以采用较高的切削速度和进给率,快速去除大量材料;而在精加工阶段,则需采用更低的切削速度和进给率,以获得更高的表面质量和尺寸精度。
5. 切削路径优化
优化切削路径可以减少不必要的工具运动和空转时间,降低切削力和工具磨损。采用合适的切削路径规划软件或功能可以帮助实现最佳路径。
6. 合理的夹持和定位
良好的夹持和定位方案可以确保工件稳定性和加工精度。在编程过程中考虑夹具的设计和使用,以最大程度地减少工件重定位次数,并确保加工的一致性和准确性。
7. 刀具路径优化
优化刀具路径可以减少不必要的刀具移动,降低加工时间和工具磨损。避免过度切削和重复切削,并确保刀具路径的连续性和稳定性。
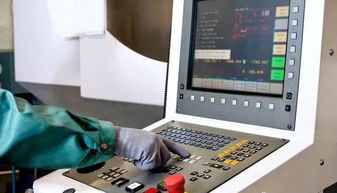
8. 转速和进给率的优化
根据加工材料和刀具特性,优化切削参数(如转速和进给率)是提高加工效率和质量的关键。通过试验和仿真,确定最佳的切削参数组合。
结论
优化机床编程顺序是提高生产效率和产品质量的重要步骤。通过工序分析、合理的刀具选择、分层加工策略、先粗后精原则、切削路径优化、夹持和定位、刀具路径优化以及转速和进给率的优化,可以实现最佳的编程顺序,提高加工效率,降低成本,提高竞争力。
版权声明
本文仅代表作者观点,不代表百度立场。
本文系作者授权百度百家发表,未经许可,不得转载。