钻孔基本编程原理与技巧解析
钻孔基本编程是指在数控钻床或钻铣床上对工件进行钻孔操作时所需的编程技术。下面将为您介绍钻孔基本编程的原理与技巧。
一、编程原理
1. 坐标系设定:钻孔编程通常使用绝对坐标系进行程序编写。需要确定工件坐标系和机床坐标系的关系,通常采用以工件中心、孔中心或其他基准点为参考,确定机床坐标系原点的方法。
2. 加工尺寸设定:根据工程要求和工件图纸,确定所需钻孔的直径、深度和间距等加工尺寸。
3. 选取合适的钻头:根据加工要求和工件材料的硬度,选取合适的钻头。钻头的直径和长度要与所需孔径和孔深相匹配。
4. 速度和进给设定:根据工件材料的硬度和钻头的类型,合理设定钻头的转速和进给速度,以确保加工质量和效率。
5. 进给和转速修正:为了提高加工效率和质量,可以根据实际加工情况进行进给和转速的修正。例如,对于较深的孔,可以适当调整进给速度以避免切屑堵塞。
二、编程技巧
1. G代码的运用
G81:钻孔循环,定义钻孔的深度、进给和快速退刀距离。
G83:深孔钻孔循环,与G81类似,但有快速提刀的功能。
G98:循环进给的起点设定,用于设定循环钻孔的起始位置。
G99:循环进给的终点设定,用于设定循环钻孔的终止位置。
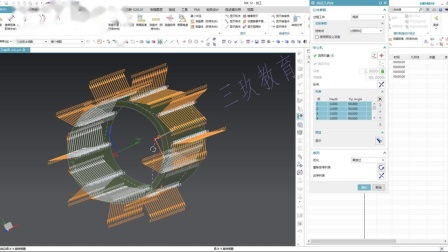
2. 刀具补偿的使用
偏移补偿 G41/G42:根据钻头半径进行偏移补偿,以保证钻孔位置准确。
长度补偿 G43/G44:根据钻孔的深度进行长度补偿,以避免钻头卡住或深度不足。
3. 循环钻孔的应用
循环钻孔可以大幅提高钻孔的加工效率。通过设置循环钻孔的步长和圈数,实现连续的钻孔操作。
针对不同孔径的钻孔,可以使用循环钻孔的方式,减少编程代码量和加工时间。
4. 安全措施
在编程过程中,要考虑到机床和工件的安全性,避免碰撞和误操作。
确保刀具和夹具的刚性和稳定性,以防止振动和失衡。
三、编程注意事项
1. 下刀深度和进给速度要合理选择,避免过快或过慢导致切削质量下降或刀具破损。
2. 钻头不宜长时间连续加工,应适当冷却,以防止钻头过热损坏。
3. 在编写钻孔程序时,注意检查程序的正确性和合理性,避免出现错误和危险操作。
4. 在加工过程中,定期检查刀具磨损情况,及时更换或修整刀具,保持加工质量。
钻孔基本编程涉及坐标系设定、加工尺寸设定、选取钻头、速度和进给设定、G代码运用、刀具补偿、循环钻孔和安全措施等方面。合理应用编程原理与技巧,可提高钻孔加工的效率和质量,确保工件的加工要求。在实际操作中,需要根据具体情况进行调整和优化,提升工作效率和钻孔质量。
版权声明
本文仅代表作者观点,不代表百度立场。
本文系作者授权百度百家发表,未经许可,不得转载。